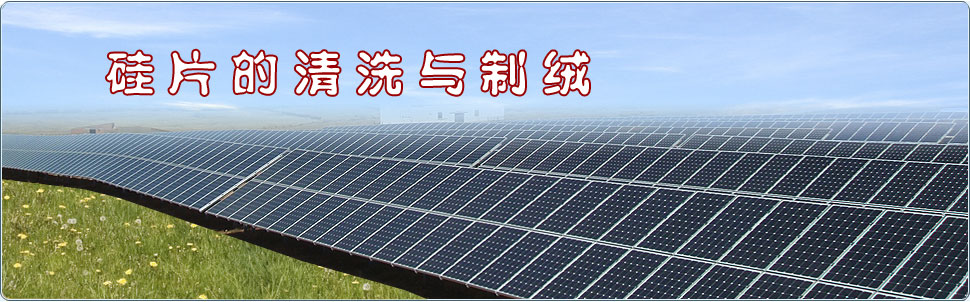
![]() |
导语:硅片在经过一系列的加工程序之后需要进行清洗,清洗的目的是要消除吸附在硅片表面的各类污染物,并制做能够减少表面太阳光反射的绒面结构(制绒),且清洗的洁净程度直接影响着电池片的成品率和可靠率。制绒是制造晶硅电池的第一道工艺,又称“表面织构化”。有效的绒面结构使得入射光在硅片表面多次反射和折射,增加了光的吸收,降低了反射率,有助于提高电池的性能。 |
一.清洗
|
二.制绒
1.制绒的目的和原理 |
|||||||
目的:减少光的反射率,提高短路电流(Isc),最终提高电池的光电转换效率。 |
②多晶硅:利用硝酸的强氧化性和氢氟酸的络合性,对硅进行氧化和络合剥离,导致硅表面发生各向同性非均匀性腐蚀,从而形成类似“凹陷坑”状的绒面,如图3所示。 |
||||||
图2 电子显微镜下的多晶硅表面绒面效果 |
图3 电子显微镜下的多晶硅表面绒面效果 |
||||||
以单晶硅绒面为例,金字塔形角锥体的表面积S等于四个边长为a的正三角形面积之和,可计算得表面积s为: |
即绒面表面积比平面提高了1.732倍。如图4所示,光线在表面的多次反射,有效增强了入射太阳光的利用率,从而提高光生电流密度。既可获得低的表面反射率,又有利于太阳能电池的后续制作工艺。
|
||||||
图4 光线在绒面中的多次反射 |
图5 单晶硅片制绒前后的表面反射率对比 |
||||||
2.制绒工艺 |
|||||||
目前在大工业生产中一般采用成本较低的氢氧化钠或氢氧化钾稀溶液(浓度为1%~2%)来制备绒面,腐蚀温度为80℃±5℃。另外,为了有效地控制反应速度和绒面的大小,会添加一定量的IPA作为缓释剂和络合剂。
|
图6 较为理想的绒面效果图 |
||||||
3.影响绒面质量的关键因素 |
|||||||
|
三.制绒设备设计要点
单晶硅的绒面制备,能够有效地提高电池转换效率,由于市场的变化,对绒面质量的要求也变的越来越高,如何做出高质量的绒面,不仅仅是工艺技术的问题,还需要与优异的设备进行配合,而设备的相关性能也决定了工艺的效果。
|
SFQ一1508ZT型全自动制绒清洗设备
|
设备共配置14个工艺槽位(除上、下料位外),用户在手动上料后全过程由三套机械传动装置完成腐蚀、清洗等工艺过程,全过程自动化,减少人工干预。设备具有自动化程度高,运行成本低,生产效率高、性能稳定、安全可靠等特点。用户可根据工艺要求通过在线的工艺设置软件,对各槽相应工艺参数进行设置,包括液体温度、腐蚀/清洗工艺时间、工艺设置、鼓泡功能设置、手动/自动转换等,系统提供故障检测、报警信息、历史记录、维护信息等详尽的记录。 |
(2)制绒槽的结构优化设计 |
|
考虑到制绒工艺段对整个生产线的重要作用,针对影响制绒反应的因素,对设备工艺段的设计进行更加精细的调整: 2.考虑到在实际生产中,操作人员要经常更换溶液,为了保证整条工艺线的生产效率,对于加热系统的容量也做了仔细的考量。加热功率过高,会引起槽内溶液温度波动太大;功率太小则可能造成每次换液后溶液升温时间过长影响生产效率。考虑这种情况,我们采用在线加热方式实现换液时直接注入70℃左右的DI水,槽内配置12 kW的加热管,以实现维持工艺温度的要求。相比传统的外接DI水预热槽的方式,在线加热方式具有升温快(3 min内可实现将流量为3.5 L/min的DI水由室温升至70℃,后续持续保持出水温度在70℃左右)、体积小(可安装在设备内部,减少净化厂房占地面积)、对DI水电阻率影响小(在线方式可最大限度地降低DI水因长时间储存而引起的电阻率下降等问题)等优势。有效的减少生产过程的配液时间,提高了生产效率。 3.槽体结构对溶液均匀性的影响,主要包括循环系统分布的均匀性和N:鼓泡的细密性,对工艺槽内硅片绒面质量的稳定性及均匀性有很大影响。循环系统包括循环入口、循环泵、管路系统、底部多通道注入管及匀流隔板等。选用进口磁力循环泵及进口PP管件,保证循环系统的效果及洁净度。底部的多通道注入管及匀流隔板设计保证了循环效果的均匀性,循环角度可根据需要进行调整。经实际工艺验证,循环功能启动后溶液以平稳的波纹状实现循环。循环的角度全面,流向与硅片平行。同时N:鼓泡功能细密,能够覆盖硅片所在的所有区 |
|
通过对整个工艺运行的跟踪了解,硅片在平移、提升运动中需要整体考虑机械臂运行稳定性,同时在平稳运行的前提下尽可能的减少硅片暴露在空气中的时间。为了防止平移/提升过程中由于水分挥发在硅片表面产成水纹印,在制绒段的机械手臂上安装了可根据工艺要求设置的DI水喷淋装置,当料篮从溶液中提出后,喷淋装置启动,DI水以雾状方式喷射,保证了硅片各个角度都可以喷淋到,尤其是硅片与料篮接触的部分,经过喷淋后可有效避免出现“边缘花片”的情况。 |